Benefits of Medical Injection Molding
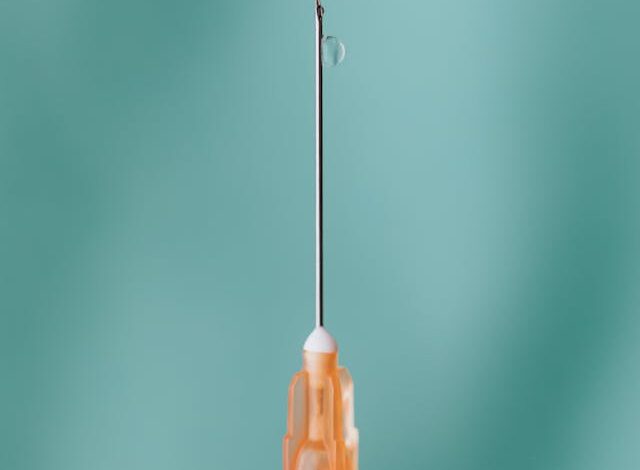
Introduction to Medical Injection Molding
In the realm of modern healthcare, precision is paramount. From intricate surgical instruments to life-saving implants, the accuracy and reliability of medical devices can make all the difference. Medical injection Molding stands at the forefront of manufacturing processes, ensuring the production of high-quality, precise components that are integral to the functioning of medical equipment.
Importance of Precision in Medical Devices
The medical field demands nothing short of perfection when it comes to device performance. Whether it’s a catheter delivering medication or a complex implant tailored to fit a patient’s anatomy, precision is non-negotiable. Medical Injection Molding plays a pivotal role in meeting these stringent requirements, enabling the creation of intricate components with unparalleled accuracy.
Benefits of Medical Injection Molding
a. Cost-effectiveness
One of the primary advantages of medical injection Molding is its cost-effectiveness. The ability to mass-produce components with minimal waste results in significant cost savings for manufacturers. Additionally, the scalability of the process allows for efficient production, further driving down expenses.
b. Design Flexibility
Medical injection Molding offers unparalleled design flexibility, allowing for the creation of complex geometries and intricate features that would be challenging or impossible to achieve through traditional manufacturing methods. This versatility enables engineers to optimize device performance and functionality while adhering to strict size and weight constraints.
c. Material Selection
From biocompatible polymers to high-performance thermoplastics, medical injection Molding accommodates a wide range of materials suitable for medical applications. This flexibility in material selection allows for tailored solutions that meet the specific needs of each device, whether it requires enhanced strength, flexibility, or biocompatibility.
d. Speed and Efficiency
In an industry where time can be a matter of life and death, the speed and efficiency of medical injection Molding are invaluable. With rapid cycle times and high throughput capabilities, manufacturers can quickly produce large quantities of components without sacrificing quality or precision.
e. Consistency and Quality Control
Consistency is paramount in medical device manufacturing, where even minor variations can have serious consequences. Medical injection Molding ensures uniformity and precision across every component, minimizing variability and enhancing quality control measures.
f. Reduced Waste
Unlike traditional machining or casting processes, Medical Injection Molding generates minimal waste. The ability to precisely control material usage and optimize part designs results in minimal scrap, reducing environmental impact and lowering production costs.
g. Sterilization Compatibility
Medical devices must undergo rigorous sterilization procedures to ensure patient safety. Components produced through medical injection Molding are compatible with various sterilization methods, including autoclaving, gamma irradiation, and ethylene oxide sterilization, maintaining product integrity and functionality.
Case Studies: Real-world Applications
Medical injection Molding finds widespread use across a diverse range of medical devices, including surgical instruments, implants, and drug delivery systems.
a. Surgical Instruments
From scalpel handles to forceps, medical injection Molding produces precision instruments essential for surgical procedures. The ability to create complex, ergonomic designs enhances surgeon comfort and facilitates more precise movements during delicate operations.
b. Implants and Prosthetics
Implants and prosthetics demand the utmost precision to ensure proper fit and functionality within the human body. Medical injection Molding enables the production of custom implants tailored to individual patient anatomy, improving patient outcomes and quality of life.
c. Drug Delivery Systems
The development of advanced drug delivery systems relies on precise engineering and manufacturing processes. Medical injection Molding allows for the creation of intricate components, such as syringes, vials, and drug-eluting implants, that optimize drug delivery and improve patient compliance.
Future Prospects and Innovations in Medical Injection Molding
As technology continues to advance, so too will the capabilities of medical injection Molding. Innovations such as additive manufacturing and bioresorbable materials hold the promise of revolutionizing medical device manufacturing, offering new possibilities for customization, biocompatibility, and sustainability.
Conclusion
Medical injection Molding offers a myriad of benefits that are indispensable to the modern healthcare industry. From cost-effectiveness and design flexibility to consistency and sterilization compatibility, this manufacturing process plays a vital role in the production of high-quality, precise medical devices that save lives and improve patient outcomes.