What Kind of Plastic Is Used in Medical Injection Molding?
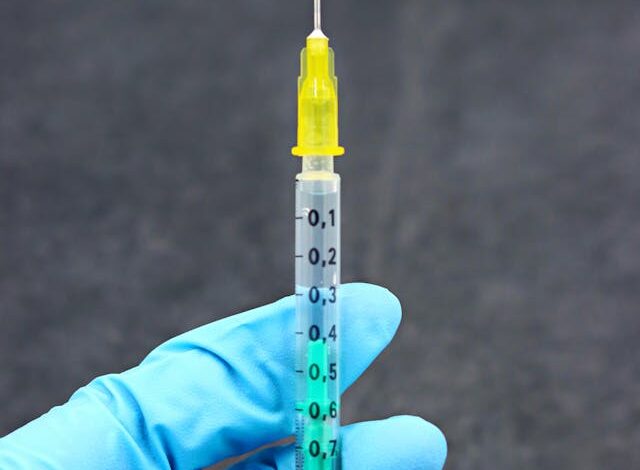
Medical injection molding is a crucial process in the production of various medical devices and components. From syringes to intricate surgical instruments, the reliability and safety of these medical tools heavily rely on the materials used in their manufacturing. One of the fundamental questions in this domain is: what kind of plastic is used in medical injection molding?
In this comprehensive guide, we’ll delve into the specifics of plastics utilized in medical injection molding, their properties, and the considerations involved in selecting the most suitable material for medical applications.
Introduction to Medical Injection Molding
Medical Injection Molding is a manufacturing process wherein molten plastic is injected into a mold cavity to produce intricate medical components with high precision and repeatability. This method is favored in the medical industry due to its efficiency, cost-effectiveness, and ability to produce complex geometries.
Importance of Plastic in Medical Injection Molding
Plastic plays a pivotal role in medical injection molding, as it offers versatility, durability, and compatibility with various sterilization methods. Moreover, plastics can be engineered to meet stringent regulatory requirements and specific application needs.
Types of Plastics Used
Thermoplastics
Thermoplastics are the most commonly used materials in medical injection molding due to their ability to be melted and re-molded multiple times without undergoing chemical degradation. This property makes them ideal for applications requiring intricate designs and tight tolerances.
Thermosets
While less common than thermoplastics, thermoset plastics are also used in medical injection molding. These materials undergo irreversible curing upon heating, resulting in enhanced strength and chemical resistance.
Common Plastics in Medical Injection Molding
Polypropylene (PP)
PP is widely used in medical devices such as syringes, vials, and containers due to its excellent chemical resistance, low cost, and ease of processing.
Polyethylene (PE)
PE is known for its flexibility, impact resistance, and biocompatibility, making it suitable for applications like medical tubing and packaging.
Polystyrene (PS)
PS is favored for its clarity, rigidity, and ease of sterilization, making it ideal for medical components like petri dishes and test tubes.
Polyvinyl Chloride (PVC)
PVC is valued for its durability, chemical resistance, and affordability, making it a common choice for medical tubing, IV bags, and blood bags.
Polycarbonate (PC)
PC offers exceptional impact strength, heat resistance, and transparency, making it suitable for medical applications requiring high-performance materials.
Criteria for Selecting Plastic in Medical Injection Molding
Selecting the right plastic for medical injection molding involves considering various factors, including:
Biocompatibility
Plastics used in medical devices must be biocompatible to ensure they do not elicit adverse reactions when in contact with bodily tissues or fluids.
Sterilization Compatibility
Medical devices often require sterilization, so the chosen plastic should withstand common sterilization methods such as steam, ethylene oxide, and gamma irradiation.
Chemical Resistance
Plastics must resist degradation when exposed to harsh chemicals commonly used in medical settings to maintain their integrity and functionality.
Challenges and Considerations
Regulatory Compliance
Medical plastics must adhere to stringent regulatory standards such as ISO 10993 and USP Class VI to ensure patient safety and product efficacy.
Material Properties
Understanding the mechanical, thermal, and chemical properties of plastics is essential for selecting the most suitable material for a specific medical application.
Cost
Balancing performance requirements with cost considerations is crucial in medical injection molding to ensure affordability without compromising quality or safety.
Future Trends in Plastic Use for Medical Injection Molding
Advancements in material science and manufacturing technologies are driving innovations in medical plastics, leading to the development of novel materials with enhanced properties and functionalities.
Conclusion
In conclusion, the choice of plastic in Medical Injection Molding is a critical decision that directly impacts the safety, efficacy, and performance of medical devices. By understanding the properties, requirements, and considerations involved, manufacturers can select the most suitable plastic for their specific application needs.
FAQs
1. Can recycled plastics be used in medical injection molding?
Yes, some medical-grade plastics are available in recycled forms, provided they meet the necessary regulatory requirements and quality standards.
2. How do regulatory standards influence the selection of plastics for medical injection molding?
Regulatory standards dictate the biocompatibility, sterilization compatibility, and chemical resistance requirements that plastics must meet to ensure patient safety and regulatory compliance.
3. What role does material testing play in selecting plastics for medical injection molding?
Material testing helps assess the mechanical, thermal, and chemical properties of plastics to determine their suitability for specific medical applications and environments.
4. Are there any environmentally friendly alternatives to traditional plastics used in medical injection molding?
Yes, biodegradable and bio-based plastics are emerging as sustainable alternatives to traditional petroleum-based plastics in medical injection molding.
5. How can manufacturers ensure the traceability of plastics used in medical injection molding?
Implementing robust quality management systems and tracking mechanisms enables manufacturers to trace the origin, composition, and processing history of plastics used in medical devices.