What Types of Medical Products are Ideal for Injection Molding?
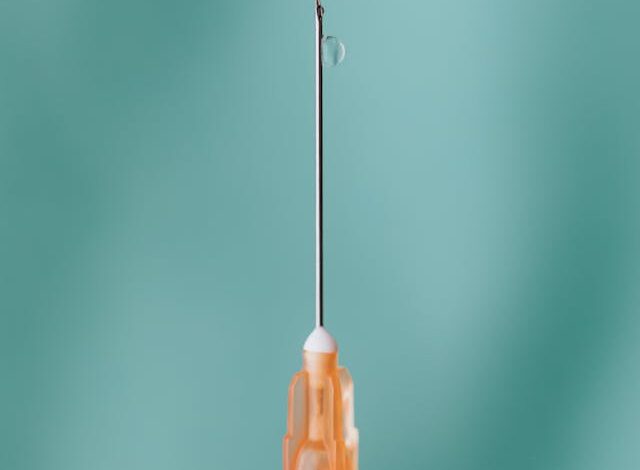
Introduction
Injection molding has revolutionized the manufacturing industry, particularly in the medical sector. Its ability to produce intricate, high-quality parts with precision and efficiency has made it the go-to method for creating various medical products. But what types of medical products are most suitable for injection molding? Let’s delve into this question.
Understanding Injection Molding
What is Injection Molding?
Medical Plastic Injection Molding is a manufacturing process where molten material is injected into a mold cavity under high pressure. Once cooled and solidified, the mold is opened to reveal the final product.
How Does Injection Molding Work?
The process begins with the material being heated and then injected into a mold cavity. The material solidifies within the mold, taking its shape. Once cooled, the mold opens, and the finished product is ejected.
Types of Medical Products Suitable for Injection Molding
Disposable Medical Supplies
Disposable medical supplies such as syringes, vials, and IV components are commonly manufactured using injection molding due to the process’s ability to produce large volumes of identical parts quickly and cost-effectively.
Medical Device Components
Various components of medical devices, including housings, connectors, and valves, are often made through injection molding. The process allows for the creation of intricate designs with tight tolerances, ensuring the reliability and performance of medical devices.
Laboratory Equipment
Injection molding is also utilized in the production of laboratory equipment such as test tubes, pipettes, and petri dishes. The method enables the mass production of high-quality, precise components essential for scientific research and experimentation.
Advantages of Injection Molding for Medical Products
Precision and Consistency
Injection molding offers unmatched precision and consistency, ensuring that each part meets strict quality standards. This is crucial in the medical field, where accuracy and reliability are paramount.
Cost-Effectiveness
The ability to produce large quantities of parts in a relatively short amount of time makes injection molding highly cost-effective for medical product manufacturing. It helps reduce per-unit costs, making medical products more accessible to healthcare providers and patients.
Complex Designs
Injection molding allows for the creation of complex geometries and intricate designs that would be difficult or impossible to achieve with other manufacturing methods. This versatility enables the production of innovative medical products that meet specific clinical needs.
Material Selection for Medical Injection Molding
Biocompatibility
When selecting materials for medical injection molding, biocompatibility is a primary consideration. The chosen materials must be safe for use in contact with the human body and should not cause any adverse reactions or toxicity.
Sterilization Compatibility
Medical products manufactured through injection molding must be compatible with various sterilization methods, including autoclaving, gamma irradiation, and ethylene oxide sterilization. The selected materials should withstand these processes without compromising their structural integrity or performance.
Regulatory Compliance and Standards
FDA Regulations
Medical products manufactured through injection molding are subject to stringent regulations set forth by regulatory bodies such as the U.S. Food and Drug Administration (FDA). Compliance with these regulations is essential to ensure the safety and efficacy of medical devices and supplies.
ISO Standards
In addition to FDA regulations, medical products must also adhere to international standards outlined by organizations like the International Organization for Standardization (ISO). These standards cover various aspects of medical device manufacturing, including quality management systems and product testing.
Challenges and Considerations
Design Complexity
Designing complex parts for injection molding can be challenging, as certain geometries may lead to issues such as warping, sink marks, or uneven shrinkage. Careful consideration must be given to part design to optimize manufacturability and minimize defects.
Material Selection Challenges
Choosing the right material for medical injection molding can be daunting, given the multitude of options available. Factors such as strength, flexibility, biocompatibility, and sterilization compatibility must all be taken into account to ensure the suitability of the material for the intended application.
Sterilization Requirements
Medical products must undergo rigorous sterilization processes to eliminate harmful pathogens and ensure patient safety. Injection-molded parts must be designed and manufactured to withstand these sterilization methods without compromising their functionality or structural integrity.
Future Trends in Medical Injection Molding
Additive Manufacturing Techniques
Advancements in additive manufacturing, such as 3D printing, are shaping the future of medical injection molding. These techniques offer greater design freedom and customization options, allowing for the creation of patient-specific medical devices and implants.
Customization and Personalization
The demand for personalized healthcare solutions is driving the development of customized medical products. Injection molding enables the mass production of bespoke components tailored to individual patient needs, improving treatment outcomes and patient satisfaction.
Integration of IoT and Smart Technologies
The integration of Internet of Things (IoT) and smart technologies into medical devices is revolutionizing patient care. Injection-molded components equipped with sensors and connectivity features enable real-time monitoring, remote diagnostics, and enhanced data collection for healthcare providers.
Conclusion
Medical Plastic Injection Molding plays a pivotal role in the manufacturing of various medical products, offering precision, cost-effectiveness, and versatility. From disposable supplies to intricate device components, injection molding enables the production of high-quality medical products that meet stringent regulatory standards and clinical requirements.