How Does the Medical Plastic Injection Molding Machine Work?
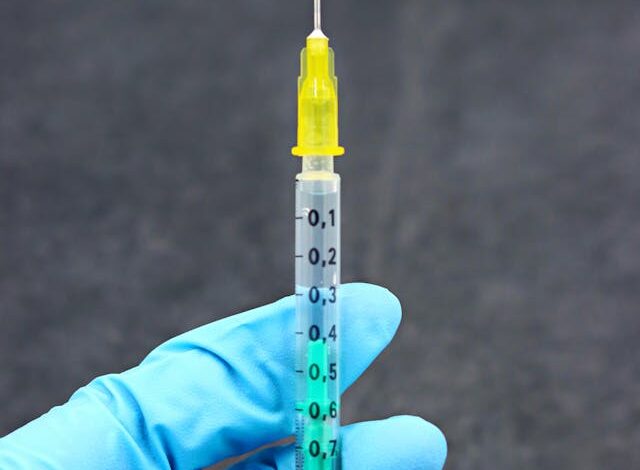
Medical plastic injection molding is a crucial process in the manufacturing of various medical devices and equipment. It involves the creation of intricate plastic components that meet the stringent requirements of the healthcare industry. But how exactly does a medical plastic injection molding machine work?
Introduction to Medical Plastic Injection Molding
Plastic injection molding is a manufacturing process that involves melting raw plastic material and injecting it into a mold cavity. In the medical field, this process is used to produce components such as syringes, IV connectors, and surgical instruments. Medical-grade plastics are essential for ensuring the safety and efficacy of these products.
Components of a Medical Plastic Injection Molding Machine
A Medical Plastic Injection Molding machine consists of several key components, each playing a crucial role in the molding process. These components include the injection unit, clamping unit, heating and cooling systems, and control system.
The injection unit is responsible for melting and injecting the plastic material into the mold cavity. The clamping unit holds the mold in place and applies pressure to keep it closed during injection. Heating and cooling systems regulate the temperature of the mold and plastic material, ensuring proper melting and solidification. The control system monitors and adjusts various parameters such as temperature, pressure, and injection speed.
Step-by-Step Process of Medical Plastic Injection Molding
The medical plastic injection molding process typically follows a series of steps:
- Mold Closing: The mold halves are closed and clamped together.
- Injection: Plastic pellets are fed into the injection unit, where they are heated and melted. The molten plastic is then injected into the mold cavity under high pressure.
- Dwelling or Cooling: Once the mold cavity is filled, the plastic material is allowed to cool and solidify. This phase is crucial for ensuring proper part formation and minimizing defects.
- Mold Opening and Ejection: After the plastic has cooled, the mold halves are opened, and the finished part is ejected from the mold cavity.
Role of Temperature and Pressure
Temperature and pressure play vital roles in the medical plastic injection molding process. Heating the plastic material to the correct temperature allows it to flow easily into the mold cavity, while applying pressure ensures that it fills the cavity completely and uniformly. Cooling the mold rapidly after injection helps to solidify the plastic material and maintain the shape of the finished part.
Quality Control Measures
Maintaining high quality is essential in medical plastic injection molding to ensure the safety and reliability of medical devices. This involves careful material selection, monitoring and adjusting process parameters, and thorough inspection of finished products to detect any defects or inconsistencies.
Applications of Medical Plastic Injection Molding
Medical plastic injection molding is used in a wide range of applications within the healthcare industry. These include the manufacturing of medical devices such as catheters, implants, and diagnostic equipment, as well as packaging for pharmaceutical products.
Advantages of Medical Plastic Injection Molding
The precision and consistency of injection molding make it an ideal manufacturing process for medical applications. It offers cost-effective production of complex parts with intricate geometries and can accommodate a wide range of materials, including specialized medical-grade plastics.
Challenges and Considerations
While medical plastic injection molding offers numerous benefits, there are also challenges and considerations to be aware of. Regulatory compliance, material compatibility, and maintenance and calibration of equipment are all critical factors that must be addressed to ensure quality and safety in medical device manufacturing.
Recent Technological Advancements
Advancements in technology continue to drive innovation in medical plastic injection molding. Automation and robotics are being increasingly integrated into the manufacturing process, improving efficiency and productivity. Additionally, the emergence of 3D printing technology offers new opportunities for rapid prototyping and customized production.
Future Trends in Medical Plastic Injection Molding
Looking ahead, the future of medical plastic injection molding holds exciting possibilities. Trends such as personalized medicine, miniaturization of medical devices, and enhanced biocompatibility are expected to drive further innovation in the field, opening up new avenues for improving patient care and treatment outcomes.
Environmental Impact and Sustainability
As the healthcare industry strives to become more environmentally sustainable, efforts are being made to reduce the environmental impact of plastic injection molding. This includes initiatives to increase recycling rates, develop biodegradable materials, and implement energy-efficient processes.
Training and Education in Plastic Injection Molding
Training and education play a crucial role in ensuring the quality and safety of Medical Plastic Injection Molding. Certification programs, hands-on training, and continuous learning opportunities help to equip professionals with the skills and knowledge needed to excel in this field.
Case Studies and Success Stories
Numerous case studies and success stories highlight the impact of medical plastic injection molding on healthcare delivery. From innovative new devices to improved patient outcomes, these examples underscore the importance of this manufacturing process in shaping the future of medicine.
Conclusion
In conclusion, medical plastic injection molding plays a vital role in the manufacturing of medical devices and equipment. By understanding the process and its components, as well as the challenges and advancements in the field, we can ensure the continued production of high-quality, safe, and effective medical products.