Various Types of Sheet Metal Bending
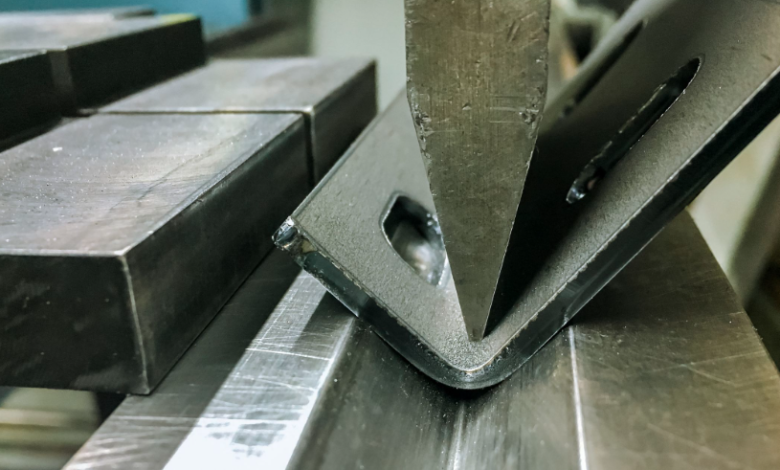
Sheet metal bending is a vital process in manufacturing and fabrication, allowing the transformation of flat metal sheets into specific shapes. This technique is widely used in industries such as construction, automotive, and aerospace, enabling the creation of components like brackets, enclosures, and frames.
There are multiple types of sheet metal bending, each offering unique advantages based on the material properties, required bend angles, and precision needs. This article explores different bending techniques, their working principles, applications, benefits, and challenges.
What is Sheet Metal Bending?
Sheet metal bending is a cold-forming process that alters the shape of a metal sheet by applying force, usually using specialized machinery like press brakes, rollers, and dies. Unlike cutting or welding, bending does not remove material; instead, it deforms the sheet to the required angle or curve.
The efficiency and accuracy of bending depend on factors such as material type, thickness, bend radius, and tooling precision. Choosing the right bending method ensures better structural integrity and minimizes production errors.
Common Types of Sheet Metal Bending
Different bending techniques are used in manufacturing, each catering to specific design and structural requirements. Below are the most common types of sheet metal bending and their applications.
1. V-Bending
V-bending is the most commonly used bending technique. It involves pressing a metal sheet into a V-shaped die using a punch, forming a precise bend.
Types of V-Bending:
- Air Bending: The punch does not fully press the sheet into the die, allowing flexible bend angles with minimal force.
- Bottoming: The sheet is completely pressed into the die, ensuring consistent angles with reduced springback.
- Coining: High pressure imprints the punch shape into the sheet, achieving highly accurate bends.
Applications:
- Automotive parts
- Metal furniture frames
- Industrial equipment
2. U-Bending
U-bending is similar to V-bending but uses a U-shaped die to create curved bends instead of sharp angles. This technique is used in applications requiring rounded bends for tubing and pipe fittings.
Applications:
- Fluid transport pipes
- Electrical enclosures
- Metal framework structures
3. Roll Bending
Roll bending is used for large-radius bends and curved shapes. The metal sheet is passed through a series of rotating rollers to form cylindrical or curved designs.
Applications:
- Tank and pipe manufacturing
- Large metal frameworks
- Curved metal components in architecture
4. Wipe Bending
Wipe bending uses a wiping die to hold the metal sheet while a punch applies force, creating a sharp bend. This method is ideal for tight, accurate bends.
Applications:
- Sheet metal panels
- Door frames
- HVAC ductwork
5. Rotary Bending
Rotary bending uses a special rotating die that bends the sheet without causing surface damage. This method is widely used in applications requiring a smooth, polished finish.
Applications:
- Aerospace components
- Decorative metal products
- High-precision machinery
6. Hemming
Hemming folds the metal sheet onto itself, creating a reinforced edge. This method improves strength and safety by eliminating sharp edges.
Read also: How Smartwatches Help Entrepreneurs Manage Business Efficiently
Applications:
- Automotive doors and panels
- Kitchen appliances
- Metal furniture edges
7. Curling
Curling forms a rolled edge on the sheet metal to improve aesthetics and safety. The metal is bent into a loop or circular shape, eliminating sharp edges.
Applications:
- Decorative trims
- Automotive components
- Structural reinforcements
8. Step Bending
Step bending, also called bump bending, creates gradual curves by performing multiple small bends in succession. This technique is an alternative to roll bending for creating large-radius bends.
Applications:
- Aerospace industry
- Custom metal designs
- Structural supports
9. Flanging
Flanging involves bending the edge of a metal sheet at a specific angle, often used for joining metal parts. It helps increase the strength of the metal part Types of Sheet Metal Bending and allows easy assembly.
Applications:
- Automotive body panels
- Electrical enclosures
- Industrial machinery
Factors Affecting Sheet Metal Bending
The effectiveness of sheet metal bending depends on several key factors:
1. Material Type
Different metals exhibit unique bending properties. Aluminum is more flexible, while stainless steel is harder to bend due to its high strength.
2. Thickness of the Sheet
Thicker sheets require more force to bend and are prone to cracking if not handled properly.
3. Bend Radius
A smaller bend radius increases the risk of cracking, while a larger radius ensures a smoother bend.
4. Springback Effect
After bending, the metal may partially return to its original shape due to elasticity. This effect is minimized using techniques like coining or bottoming.
5. Grain Direction
Bending against the grain of the metal reduces the risk of cracks and improves flexibility.
Advantages of Different Bending Methods
Each bending technique offers distinct advantages:
- V-bending and U-bending – Best for precise angle formations.
- Roll bending – Suitable for large curved structures.
- Hemming and curling – Enhances safety and durability.
- Step bending – Allows gradual curves without specialized equipment.
Challenges in Sheet Metal Bending
Although sheet metal bending is widely used, certain challenges can arise:
- Springback issues can lead to inaccurate bends.
- Cracking and material damage occur with improper bend angles.
- Tool wear and maintenance increase production costs.
- Limited bending for thick sheets requires heavy-duty equipment.
Applications of Sheet Metal Bending
Sheet metal bending plays a crucial role in various industries, including:
1. Automotive Industry
Bending is used to create body panels, exhaust systems, and frame components.
2. Construction and Architecture
Metal bending helps in manufacturing roofing panels, support beams, and handrails.
3. Aerospace Industry
Aircraft components require high-precision bending techniques for lightweight and durable structures.
4. Electronics and Appliances
Metal enclosures, casings, and internal structural supports in electronic devices and home appliances are produced using bending techniques.
Conclusion
Understanding the types of sheet metal bending is essential for selecting the right process based on material properties, design requirements, and application needs. Techniques such as V-bending, roll bending, rotary bending, and hemming enable manufacturers to achieve precision and efficiency in metal fabrication. By using advanced machinery and automation, industries can improve product quality while reducing production costs.