Urethane casting machine: A Comprehensive Analysis
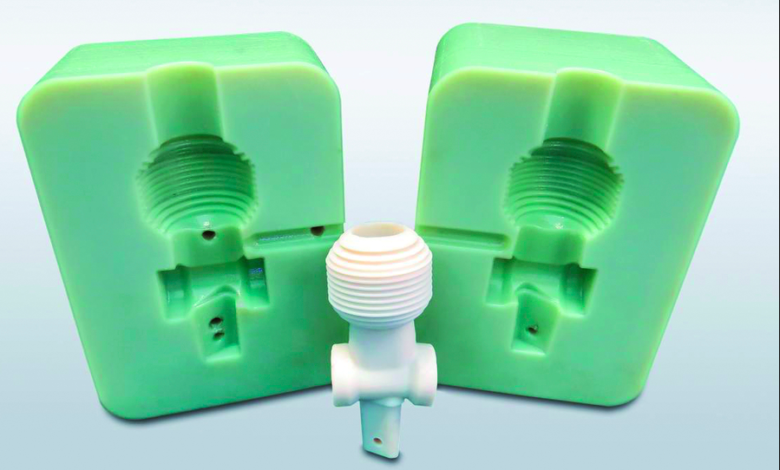
Introduction
Urethane casting is a versatile and effective method for producing high-quality parts and prototypes. Central to this process is the urethane casting machine, a critical tool that ensures the precision and efficiency of casting operations. This article explores the intricacies of Urethane casting machine, their operation, types, advantages, limitations, applications, and future trends.
Understanding Urethane casting machine
What is Urethane Casting?
Urethane casting is a manufacturing process where liquid polyurethane resin is poured into a mold to create parts or prototypes. The process is favored for its flexibility, ability to produce complex geometries, and cost-effectiveness in small to medium production runs. Urethane casting machine streamline this process by automating various stages, including mixing, pouring, and curing.
Key Components of a Urethane Casting Machine
- Resin Mixing System
- Function: This component mixes the urethane resin with hardeners or catalysts to initiate the curing process. Accurate mixing is crucial for ensuring consistent part quality.
- Types: Some machines feature manual mixing, while others offer automated mixing systems with precise controls.
- Pouring Mechanism
- Function: This mechanism transfers the mixed resin into the mold. It can be a manual pour or an automated system that ensures uniform filling and minimizes air bubbles.
- Types: Automated pouring systems can include features like vacuum degassing to remove air trapped in the resin.
- Curing Chamber
- Function: The curing chamber controls the temperature and humidity to ensure proper curing of the resin. Some machines feature built-in curing chambers, while others require external setups.
- Types: The chamber can be temperature-controlled for heat-assisted curing or room-temperature for standard curing processes.
- Demolding System
- Function: After curing, parts must be removed from the mold. This system aids in the gentle removal of parts to prevent damage.
- Types: Manual demolding involves manual handling, while automated systems use mechanisms to eject parts efficiently.
How Urethane casting machine Work
- Design and Mold Preparation
- Design: A 3D CAD model of the part is created. This model is used to design the mold, which is typically made from silicone for prototypes or metal for production runs.
- Mold Fabrication: Molds are prepared based on the design specifications. They need to be accurately machined to ensure the final part matches the design.
- Resin Preparation
- Mixing: The urethane resin is mixed with the appropriate hardeners or additives. The mixing process must be precise to ensure uniform curing and part properties.
- Degassing: To remove any trapped air bubbles, the mixed resin may be subjected to vacuum degassing before pouring.
- Casting
- Pouring: The mixed resin is poured into the mold. Automated machines often use controlled pouring systems to ensure even distribution and minimize defects.
- Curing: The filled mold is placed in a curing chamber. The curing process can vary in time depending on the resin formulation and the desired properties of the final part.
- Demolding
- Removal: After curing, the part is removed from the mold. Automated machines may have ejector systems to facilitate this process.
- Post-Processing: The part may undergo additional finishing steps such as trimming, sanding, or painting to meet final specifications.
Types of Urethane casting machine
Manual Urethane casting machine
Overview: These machines require manual operation for mixing, pouring, and demolding. They are often used in small-scale operations or for prototyping.
Advantages:
- Cost-Effective: Lower initial investment compared to automated systems.
- Flexibility: Ideal for custom or low-volume production where manual control is beneficial.
Disadvantages:
- Labor-Intensive: Requires more manual labor, which can be time-consuming.
- Consistency: Potential for variability in part quality due to human error.
Semi-Automatic Urethane casting machine
Overview: Semi-automatic machines offer a combination of manual and automated functions. They may automate mixing or pouring but require manual intervention for other steps.
Advantages:
- Improved Efficiency: Automation of certain processes reduces manual effort and increases production speed.
- Cost Savings: Less expensive than fully automatic machines while providing some automation benefits.
Disadvantages:
- Limited Automation: Some steps remain manual, which may limit overall efficiency and consistency.
Fully Automatic Urethane casting machine
Overview: These machines automate the entire casting process, from mixing and pouring to curing and demolding. They are designed for high-volume production and precision.
Advantages:
- High Efficiency: Fully automated systems enhance production speed and consistency.
- Reduced Labor: Minimal manual intervention required, leading to cost savings in labor.
Disadvantages:
- High Initial Cost: Significant investment required for purchasing and setting up fully automatic machines.
- Complexity: May require specialized training for operation and maintenance.
High-Pressure Urethane casting machine
Overview: Designed for handling high-pressure conditions, these machines are used for producing parts with high-density requirements.
Advantages:
- Enhanced Strength: Capable of producing parts with superior strength and durability.
- Precision: High-pressure conditions can improve the accuracy of complex geometries.
Disadvantages:
- Cost: Higher initial investment and maintenance costs.
- Specialized Use: Not suitable for all types of urethane casting applications.
Read also: Precision Optics Manufacturer: Pioneering Excellence in Optical Technology
Advantages of Using Urethane casting machine
Precision and Consistency
Urethane casting machine ensure precise mixing of resins and hardeners, leading to consistent part quality. Automated systems reduce the risk of human error, resulting in uniform parts with tight tolerances.
Increased Efficiency
Automated machines streamline the casting process, from mixing to demolding. This increased efficiency leads to faster production times and higher output rates, making it ideal for medium to high-volume production.
Flexibility
Urethane casting machine can be adjusted to accommodate different resin formulations and mold designs. This flexibility supports a wide range of applications, from prototyping to custom parts.
Cost-Effectiveness
While the initial investment in a urethane casting machine may be substantial, the long-term cost benefits can be significant. Automation reduces labor costs and material waste, leading to overall cost savings.
Conclusion
Urethane casting machine are a critical component of the urethane casting process, offering precision, efficiency, and flexibility for producing high-quality parts and prototypes. Understanding the different types of machines, their advantages and limitations, and their applications can help manufacturers make informed decisions about their casting operations.
As technology continues to advance, Urethane casting machine will evolve to meet new challenges and opportunities. Innovations in automation, materials, and sustainability will shape the future of urethane casting, offering exciting possibilities for the manufacturing industry.