Optimizing Design for Manufacturing in Thermoforming: Best Practices for Engineers and Designers
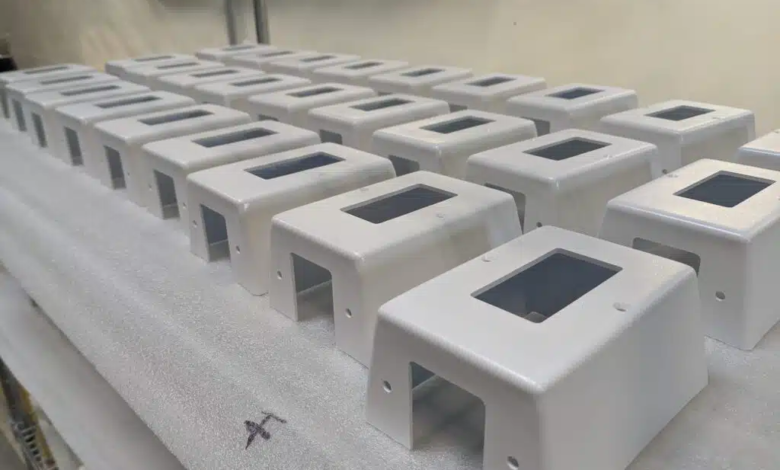
1. Introduction
Overview of Thermoforming as a Cost-Effective Manufacturing Process
Thermoforming is a widely used plastic manufacturing technique in which a thermoplastic sheet is heated to a pliable state and shaped over a mold using vacuum, pressure, or mechanical force. Once formed, the material is cooled and trimmed to create the final part. This process is prevalent in industries such as automotive, aerospace, medical, packaging, and consumer goods due to its affordability, scalability, and material versatility.
Compared to other plastic forming processes, thermoforming offers significant advantages in tooling costs and production speed, making it particularly attractive for medium-volume production and large-format parts. The method also allows for rapid prototyping and design iterations, reducing development time while maintaining functional and aesthetic performance.
Comparison to Other Manufacturing Methods
Thermoforming competes with other manufacturing processes such as injection molding, machining, and 3D printing. Each method has its strengths and limitations:
- Injection Molding: Offers superior precision and the ability to form highly intricate geometries with undercuts. However, it requires expensive tooling and long setup times, making it impractical for low- to medium-volume production.
- Machining: Provides excellent dimensional accuracy and structural integrity but generates high material waste and is not feasible for thin-walled or flexible parts.
- 3D Printing: Ideal for low-volume, highly complex, or customized parts, but lacks the speed and cost efficiency of thermoforming for mass production.
Thermoforming’s lower startup costs, faster turnaround, and ability to produce large-scale plastic components make it an optimal choice for industries requiring durable and cost-efficient plastic parts.
Importance of Design for Manufacturing (DFM) in Thermoforming
Applying Design for Manufacturing (DFM) principles in thermoforming is critical to ensuring manufacturability, quality, and cost control. Unlike injection molding, where molten material is injected into a mold, thermoforming involves stretching a pre-existing sheet of plastic. This stretching process introduces material thinning, stress distribution challenges, and mold release considerations that must be accounted for in the design phase.
Key benefits of effective DFM in thermoforming include:
- Improved Part Accuracy: Accounting for draft angles, material shrinkage, and uniform wall thickness prevents defects and ensures dimensional consistency.
- Extended Mold Life: Designing with appropriate draw ratios and feature constraints enhances mold durability and reduces maintenance costs.
- Reduced Production Costs: Optimized nesting, multi-up tooling, and material utilization lower per-unit costs while maintaining structural integrity.
By implementing these best practices, engineers and designers can optimize thermoformed components for functional performance, manufacturability, and cost-effectiveness.
2. The Thermoforming Process
Fundamentals of Thermoforming
Thermoforming is a process in which a thermoplastic sheet is heated to its softening temperature and formed over a mold using vacuum, pressure, or mechanical force. The formed sheet is then cooled and trimmed to create the final part. The process consists of four primary steps:
- Heating – The plastic sheet is heated to its forming temperature (typically between 250°F and 450°F, depending on the material).
- Forming – The softened sheet is shaped over a mold using vacuum suction, air pressure, or a mechanical plug assist.
- Cooling – The part is cooled and solidified while still on the mold to maintain its shape.
- Trimming – Excess material is trimmed, and additional finishing processes may be applied.
The thermoforming cycle varies depending on part complexity, material type, and machine capabilities. Some designs allow for multi-up production, where multiple parts are formed on a single sheet to improve efficiency and reduce per-unit costs.
Types of Thermoforming
There are three primary types of thermoforming, each suited for different applications:
1. Vacuum Forming
- The most common method, where a vacuum removes air between the plastic sheet and the mold, pulling the material tightly over the mold surface.
- Ideal for producing packaging trays, enclosures, panels, and signage.
- Cost-effective and suitable for medium- to high-volume production.
2. Pressure Forming
- Similar to vacuum forming, but with additional positive air pressure applied to push the plastic against the mold.
- Produces sharper details, finer textures, and higher precision than vacuum forming.
- Often used for applications requiring high surface quality, such as medical enclosures and consumer electronics housings.
3. Drape Forming
- The heated sheet is draped over a mold, relying on gravity or slight pressure to shape the part.
- Used for simple curved designs, large-radius bends, and aerospace applications.
- Suitable for large, lightweight structures that do not require intricate detailing.
Trimming and Finishing in Thermoforming
After the forming process, excess material must be removed, and additional features such as holes, slots, or cutouts may be added. Trimming methods include:
- CNC Trimming – Provides high-precision cuts using 3-axis or 5-axis CNC machines, ideal for complex geometries and production consistency.
- Hand Trimming – Used for prototyping or low-volume production, though it introduces variability.
- Die Cutting – Efficient for high-volume production of thin-gauge materials, offering fast and repeatable trimming.
For high-precision applications, post-trim inspections ensure dimensional accuracy, and additional finishing processes such as sanding, polishing, or surface texturing may be required.
Tooling and Mold Considerations
Molds determine the final part’s shape, surface finish, and dimensional accuracy. The choice of mold material affects cost, durability, and cycle time. Common mold types include:
- 3D-Printed Molds – Used for rapid prototyping and low-volume production; cost-effective but limited in lifespan and detail resolution.
- Machined Wood or Urethane Molds – Suitable for short runs and prototyping, offering moderate accuracy and durability.
- Machined Aluminum Molds – The industry standard for mid- to high-volume production, providing excellent precision, surface finish, and durability.
- Cast Aluminum Molds – Cost-effective for large molds, providing durability with moderate surface detail. Often includes integrated cooling lines for faster cycle times.
Mold design also impacts production efficiency, with factors such as:
- Draft Angles – Ensuring proper release from the mold to prevent defects and improve longevity.
- Undercuts – Avoiding features that complicate demolding unless necessary.
- Cooling Systems – Integrated cooling lines in aluminum molds enhance cycle time efficiency.
- Vent Holes – Preventing trapped air pockets that can lead to incomplete part formation.
Proper mold selection and design considerations significantly impact cost, cycle time, and overall part quality.
Conclusion and Next Steps
Thermoforming is a highly efficient and cost-effective manufacturing process, but achieving optimal results requires adherence to Design for Manufacturing (DFM) principles. By carefully considering material selection, mold design, forming parameters, and trimming techniques, engineers and designers can ensure high-quality, manufacturable, and cost-effective thermoformed parts.
For manufacturers seeking expert guidance in thermoforming design and production, RapidMade offers cutting-edge solutions to optimize your project. Whether you need custom thermoforming, rapid prototyping, or high-volume production, our team ensures precision, efficiency, and superior results.
🔹 Get started today! Visit RapidMade for expert DFM support and custom thermoforming solutions.